Processes
Every process step in the production of PIAD quality cast parts is undertaken in-house. This direct access to every part of the value chain guarantees the consistent high quality of PIAD cast parts.
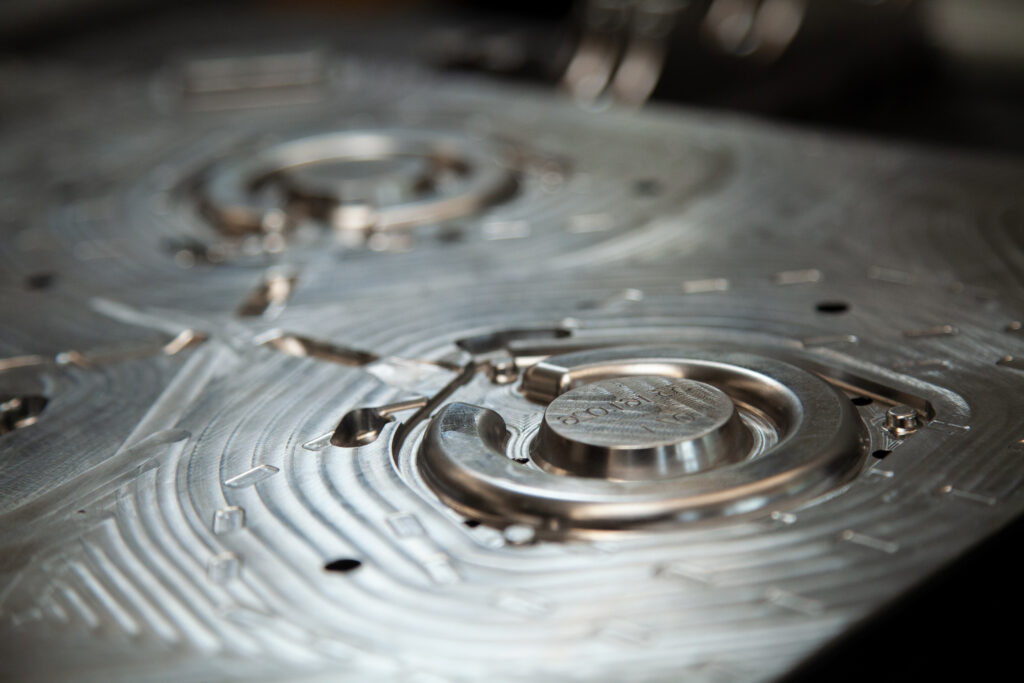
Every mould at PIAD has casting compatibility designed in, as do all aspects of the mould and tool construction. PIAD benefits from significant experience and know-how with the permanent mould casting method, and the related optimisation of casting simulation tools. Choosing the right material for the mould in relation to the cast part shape and dimensions is also extremely important.
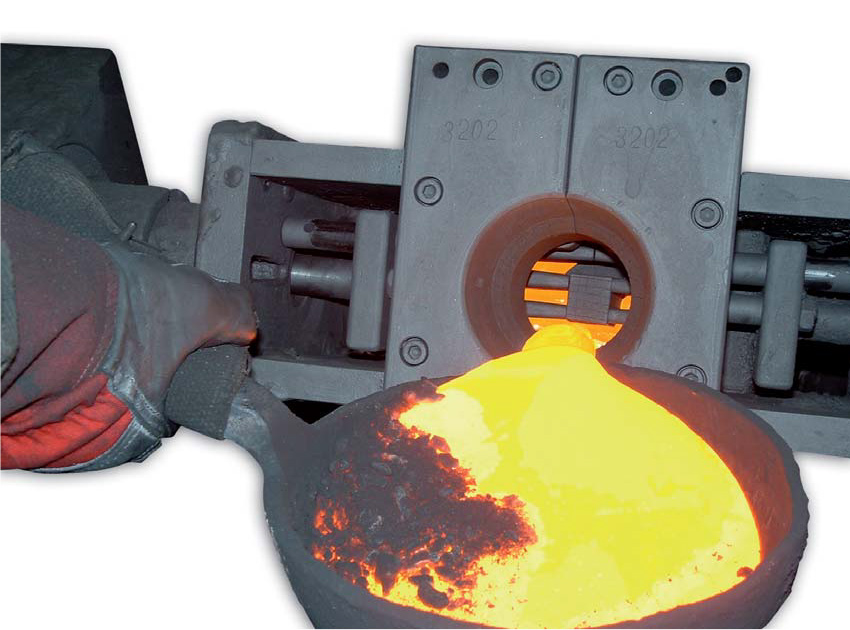
The actual casting step is of course the most important production step in the process chain. At the start of the casting process, the mould gets tilted over to present the pouring point to the caster. As the melt is poured and starts to fill, the mould is straightened up simultaneously with the rising melt level. The result is reduced shrinkage of the melt and a less turbulent filling, thus minimising air bubbles which are more commonly referred to as porosity.
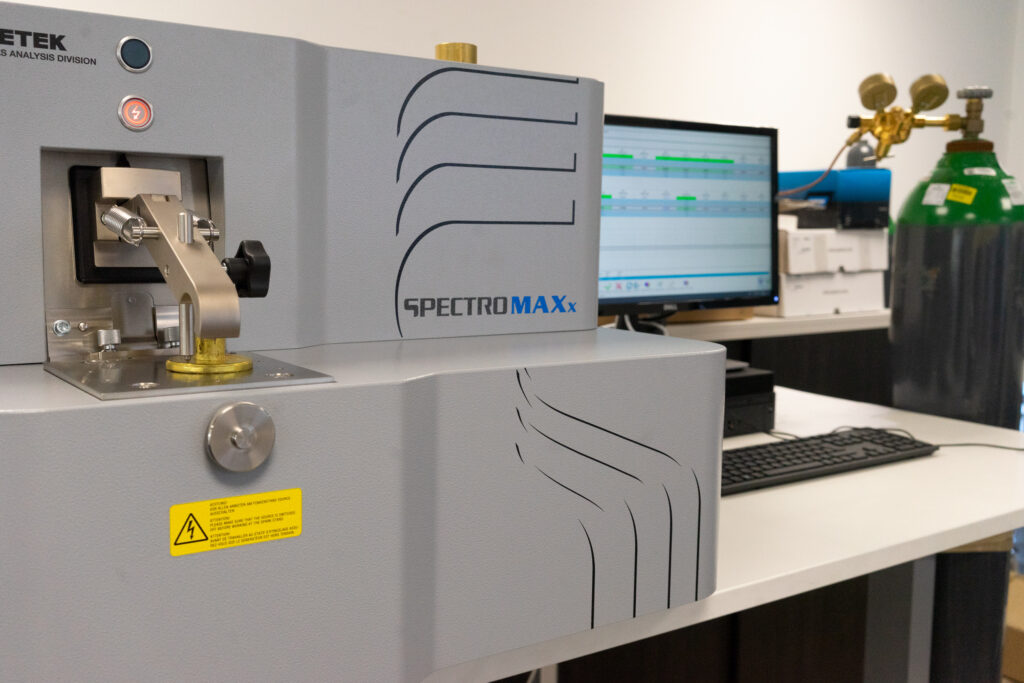
The correct formulation of the alloy within the tight parameters of the relevant PIAD standard is controlled by testing samples of the melt with a spark spectrometer on a daily basis, before and during production.
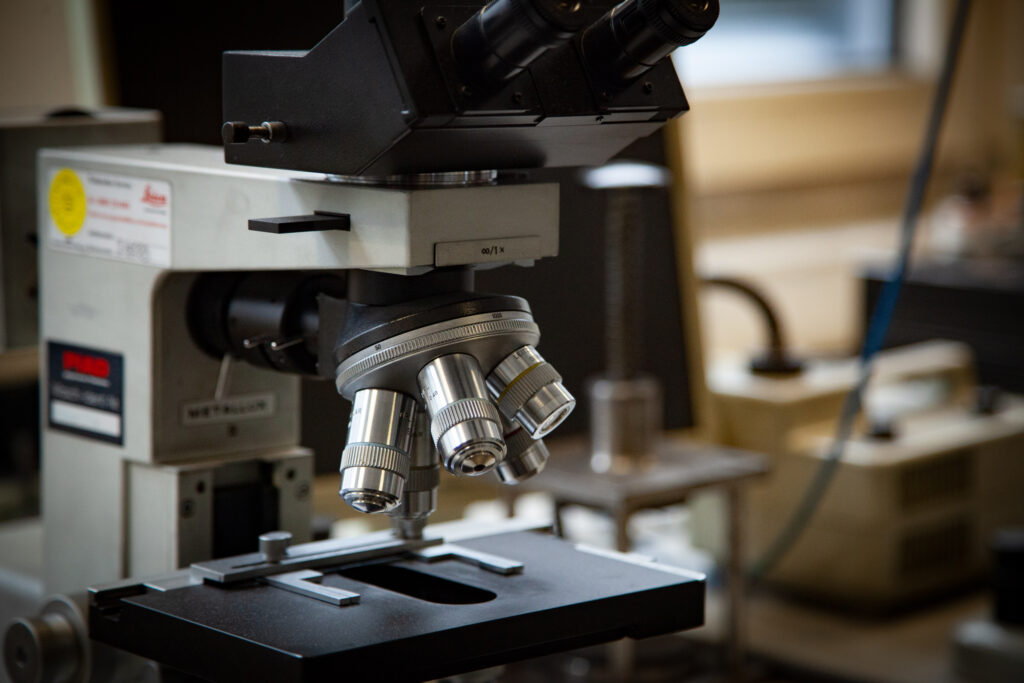
To ensure the structural quality and material performance characteristics like grain size and crystalline structure, the intermetallic phases or separations are regularly inspected during production by the metallurgical analysis of precision cut samples using metallographic examination.
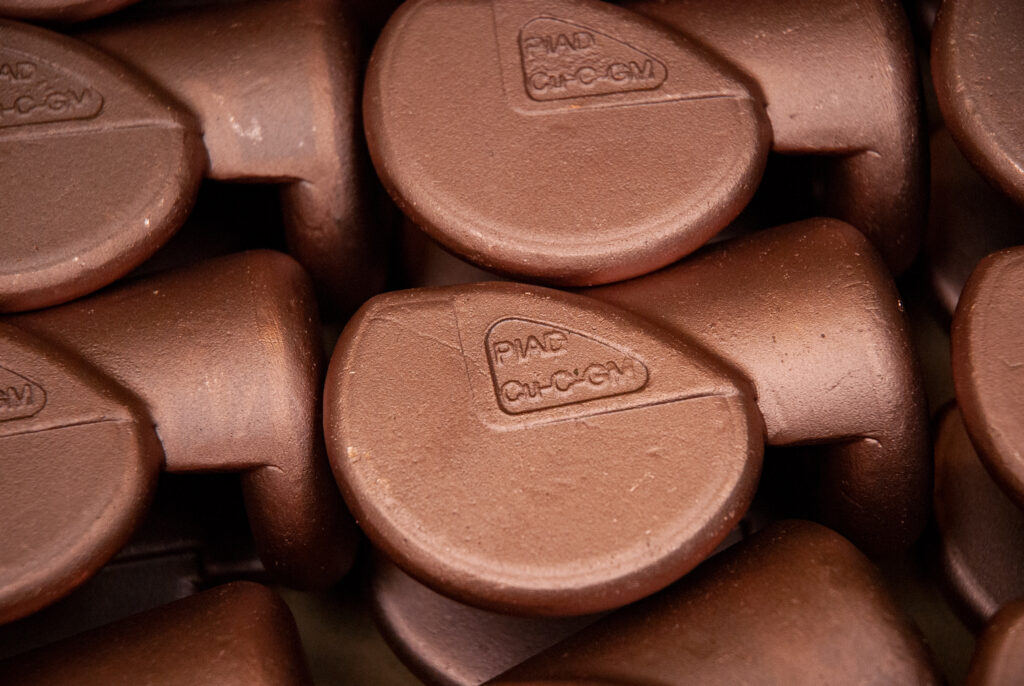
Some cast parts need to be heat treated after the casting process to achieve their final characteristics, for example parts made with copper chrome alloys.
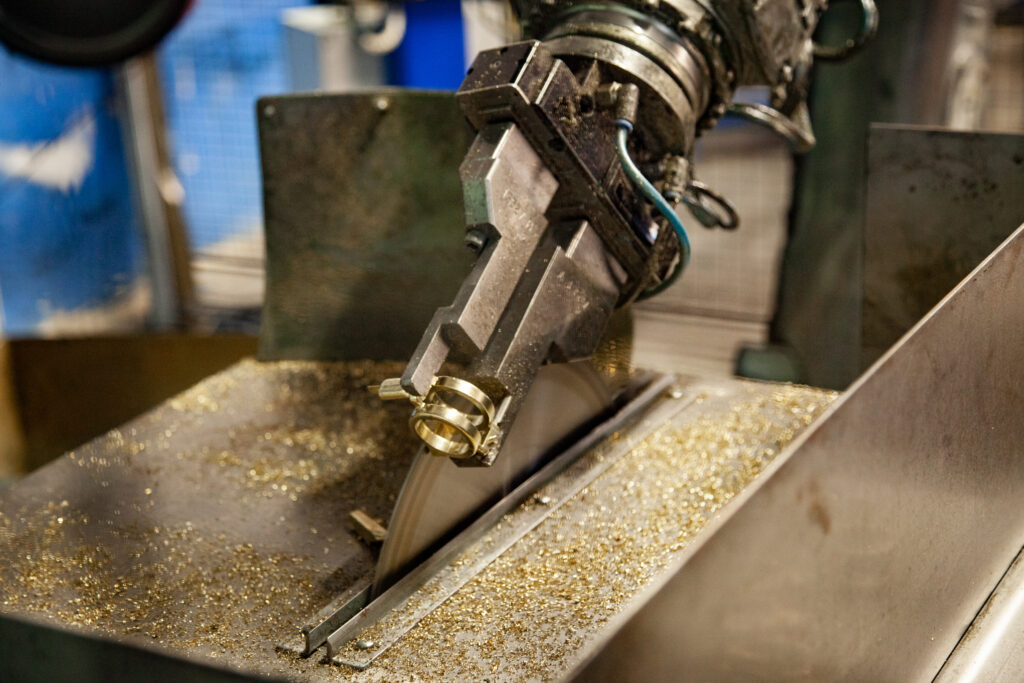
After the casting process, any feed gates and overflows have to be removed and the location ground to an agreed dimension, with any resulting burrs or flash removed. With smaller batch sizes this happens manually, but for larger production volumes the process is automated in robot cells.
Sawing
Grinding
Deburring
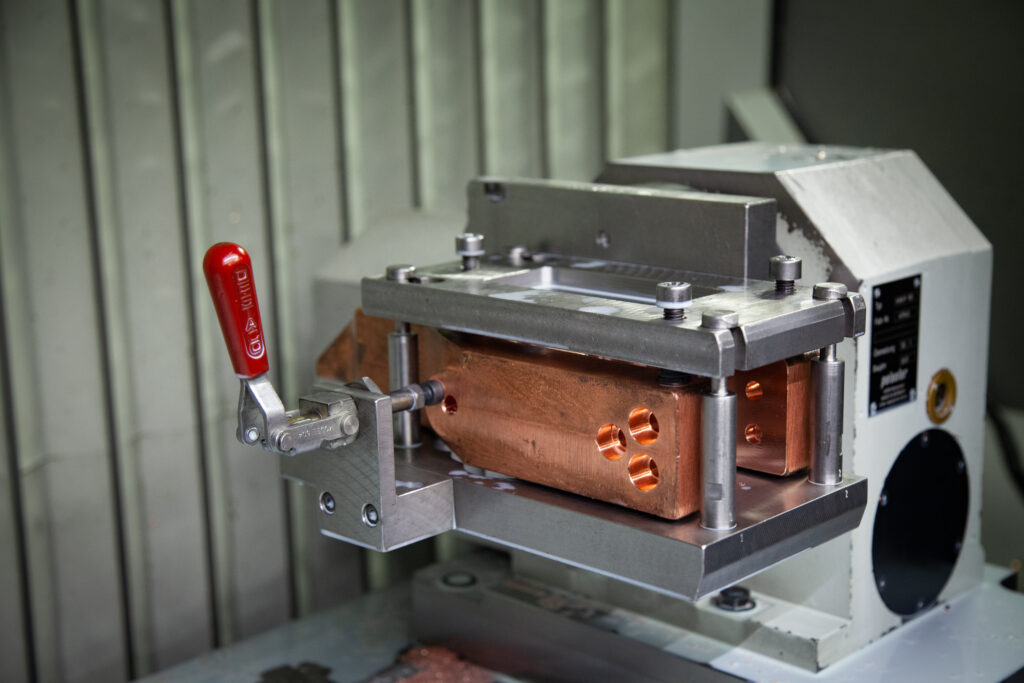
Even though it is possible to cast parts to near net shape with the permanent mould casting method, many such parts require further CNC processing to meet their specific final surface characteristics and drawing tolerances. This is also completed in-house at PIAD using modern CNC machine tools.
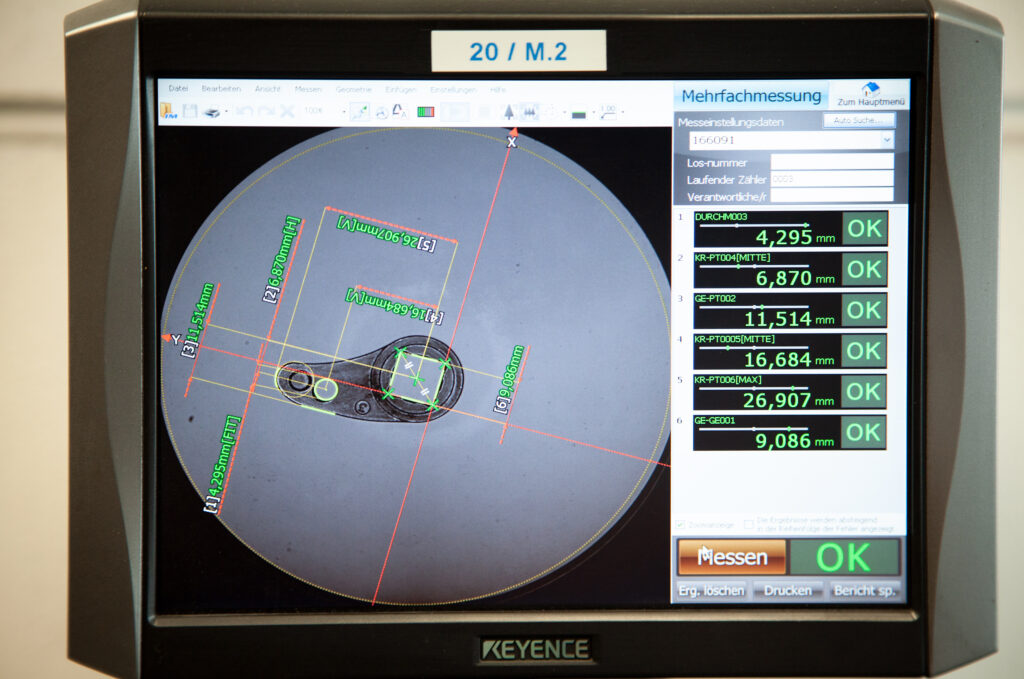
Large and thin walled cast parts have the potential risk of distortion. To ensure the parts conform to customer specifications such positional and dimensional drawing tolerances, PIAD has a modern, high quality coordinate measuring machine (CMM). This is used in conjunction with a range of other inspection devices and methods.
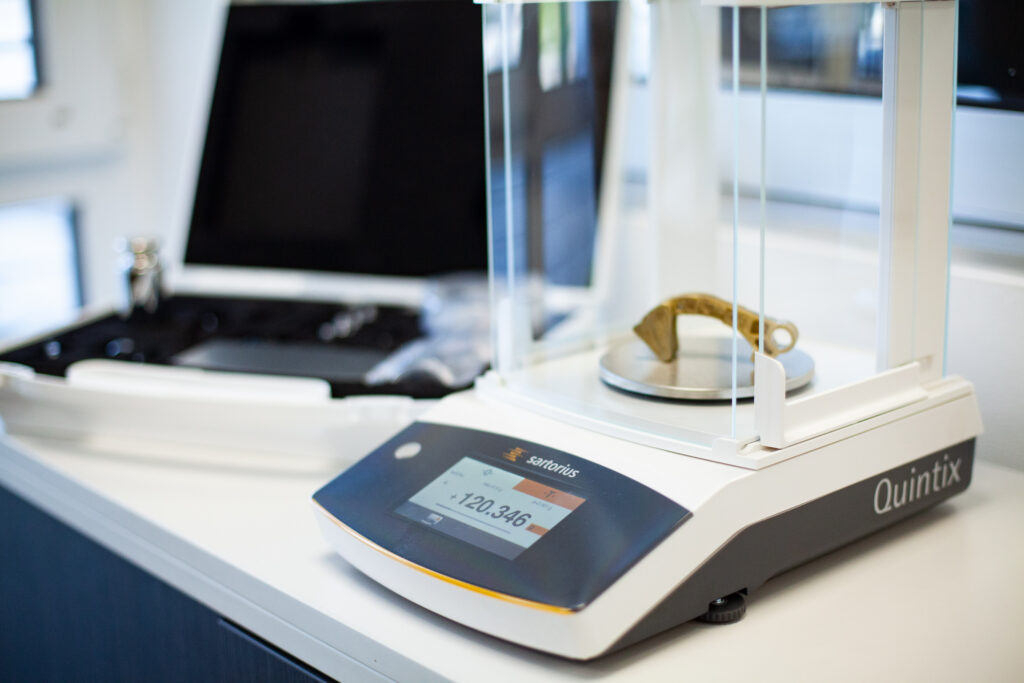
X-Ray inspection and density measurement (based upon Archimede’s Principle) of the cast parts are used to ensure a low porosity cast has been achieved, in-line with the relevant specifications.
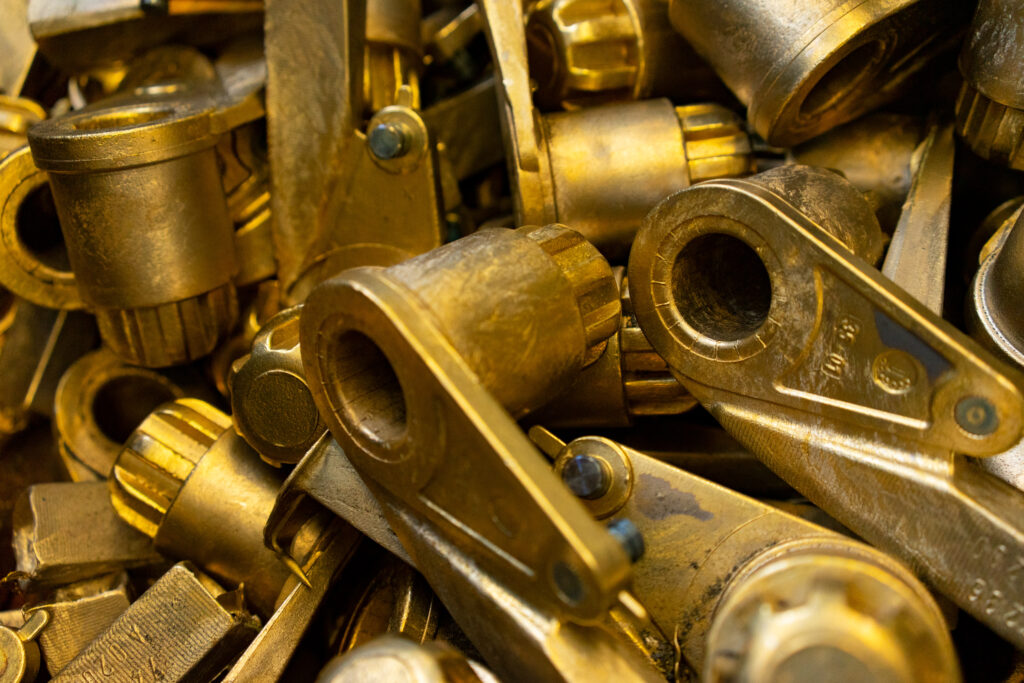
To achieve the final surface characteristics, the cast parts are barrel finished and/ or washed depending upon size and other factors.
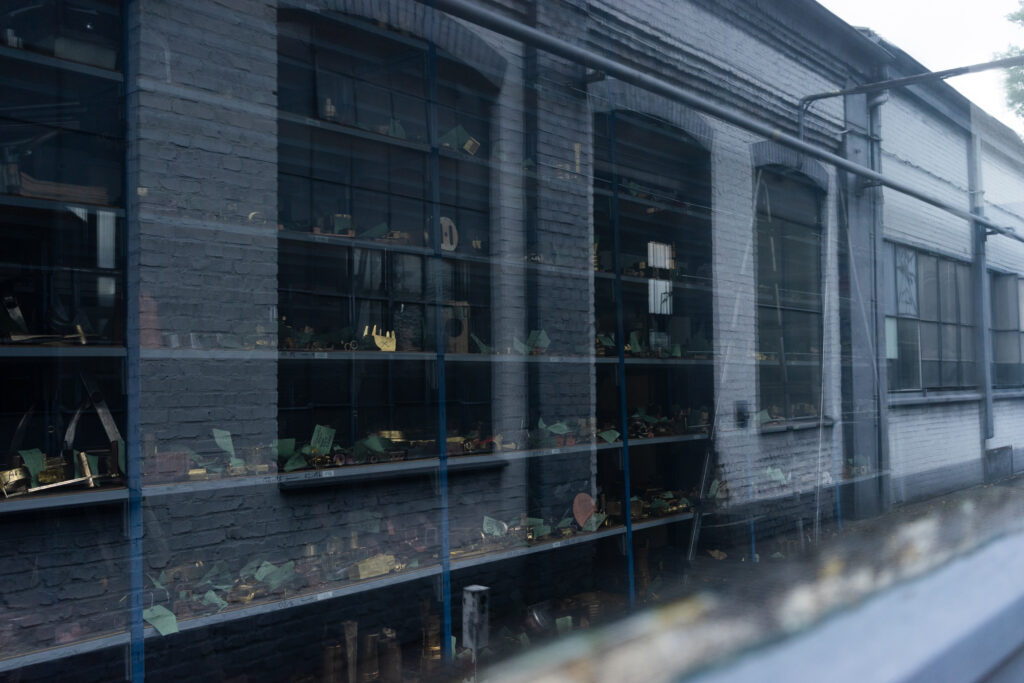
Once production of the full order quantity is complete, the mould goes into storage together with the last cast part. It possible for the customer to order further parts made with this mould over many years as PIAD will carry out any servicing, maintenance and eventual replacement of the mould according to the usage.